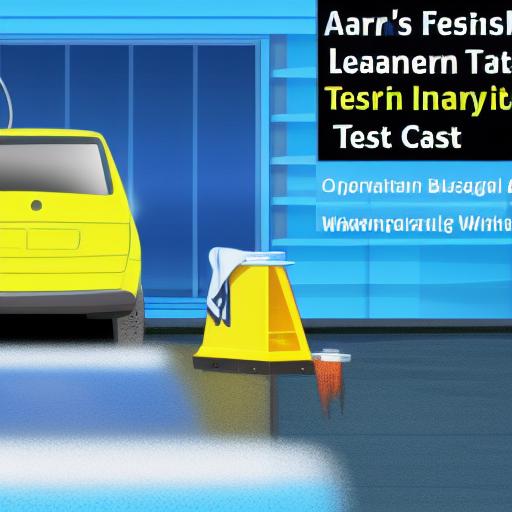
Okay, you’ve poured your heart, soul, and likely a good chunk of your savings into building your dream car wash. The gleaming bays, the fancy equipment, it’s all coming together. But before you flip that “Open” sign, there’s one crucial step you absolutely cannot skip: rigorous equipment testing. Think of it as your final exam before the real customers roll in. This isn’t just about making sure things work; it’s about preventing costly breakdowns, ensuring customer satisfaction, and ultimately, protecting your investment. Let’s dive into why, what, when, and how to thoroughly test your car wash equipment before you open your doors.
Why is Testing Your Car Wash Equipment Crucial?
Let’s get real for a second. Imagine a customer pulling into your brand-new car wash, excited for that sparkly clean finish, only to find out the soap dispenser is on the fritz or the dryer blasts out cold air. Not a great first impression, right? Here’s a breakdown of why thorough equipment testing is non-negotiable:
Avoiding Costly Downtime
A broken-down piece of equipment doesn’t just inconvenience a customer; it can grind your operations to a halt. Repair calls, replacement parts, lost revenue—it all adds up. Catching these issues during testing means you can fix them before they become a bigger headache, saving you time, money, and stress. We want your car wash to be up and running smoothly from day one.
Ensuring Customer Satisfaction
Your customers are paying for a specific service – a clean car, efficiently delivered. If your car wash equipment fails, they’re not going to get that, and they’ll likely take their business elsewhere. Testing ensures that every part of the wash process, from the pre-soak to the final wax, is executed perfectly. Happy customers become repeat customers, and that’s the foundation of any successful car wash business.
Protecting Your Investment
You’ve invested a significant amount in your car wash equipment. Regular testing helps you identify early signs of wear and tear, allowing you to maintain it properly and extend its lifespan. Think of it as preventative care for your business. A well-maintained car wash system is a long-lasting car wash system.
Upholding Brand Reputation
Word of mouth travels fast, especially in a local community. A bad initial experience can quickly damage your brand’s reputation before it even gets a chance to blossom. Properly functioning car wash equipment is crucial for presenting a professional and reliable service. Initial good impressions will help you build a strong, positive reputation.
Identifying Potential Safety Hazards
Beyond functionality, testing also helps pinpoint any potential safety hazards. Leaky hoses, improperly grounded electrical equipment, and malfunctioning safety sensors can put both your staff and customers at risk. Ensuring these issues are addressed before opening is critical for a safe and efficient operation.
What Equipment Should You Test?
Now that you understand the “why,” let’s move onto the “what.” Your car wash equipment is comprised of many interconnected parts, and each component needs to be checked thoroughly. Here’s a comprehensive checklist to get you started:
Water Systems
This is the backbone of your car wash. Thoroughly inspect:
- Water Pumps: Check for proper pressure and flow rate. Verify that all pumps are operating efficiently and consistently.
- Water Softeners: Ensure your water softener is functioning correctly and is removing the correct amount of minerals.
- Hoses & Connectors: Look for leaks, cracks, or any damage. Ensure all connections are secure and free of blockages.
- Water Nozzles: Confirm they are spraying evenly and with the correct pressure. Check that they are not clogged or damaged.
- Filtration System: Ensure the filters are clean and functioning properly. Regular checks of the filtration system will ensure clean and filtered water is being used.
Soap and Chemical Dispensers
Accurate dispensing is vital for a quality wash. Inspect:
- Soap Dispensers: Check for consistent soap output and ensure the correct dilution ratios are maintained.
- Chemical Dispensers: Verify that each chemical (e.g., pre-soak, tire cleaner, wax) is dispensed correctly.
- Delivery Lines: Inspect lines for clogs or leaks that could hinder the flow of chemicals.
- Dispensing Controls: Verify all control panels and timers are accurate and responsive.
Wash Bays
These are the heart of your operation:
- Brushes & Cloths: Check for wear and tear. Inspect all rotating parts for proper functioning. Replace any brushes or cloths that appear damaged.
- Spray Arches: Confirm they are delivering water, soap, and chemicals as intended.
- Pressure Washers: Ensure proper pressure and that the spray pattern is consistent.
- Wheel Wash System: Inspect functionality, and ensure it’s properly cleaning tires and rims.
Drying System
A crucial part of the customer experience:
- Air Blowers: Check air pressure and ensure that the dryer is operating at full capacity. Listen for any unusual noises that could indicate an issue.
- Nozzles: Confirm nozzles are clean and properly positioned for optimal drying.
- Heaters: If applicable, check that the heating elements are working and that warm air is being delivered.
Payment and Point-of-Sale (POS) Systems
Smooth transactions are critical:
- Card Readers: Verify they are reading cards accurately and processing payments correctly.
- Cash Acceptance: If applicable, ensure the bill validator is accepting various denominations and dispensing correct change.
- POS System: Test the software to make sure it is recording sales accurately. Ensure your point-of-sale system connects properly to your network and can handle customer transactions.
- Ticket Dispensers: If applicable, ensure they are dispensing tickets correctly.
Control Panels & Sensors
These are essential for automated operation:
- Main Control Panel: Ensure all buttons, switches, and displays are working properly.
- Safety Sensors: Test that all safety sensors (e.g., emergency stops, vehicle detection) are functioning correctly.
- Timers & Counters: Verify that timers and counters are accurate and functioning correctly.
- Programmable Logic Controllers (PLCs): If your equipment uses PLCs, ensure that the programs are operating smoothly.
Lighting and Signage
Often overlooked, but important:
- Bay Lighting: Ensure all lighting fixtures are functioning and provide adequate illumination.
- Exterior Lighting: Check that exterior lighting is functioning and provides adequate visibility and safety at night.
- Signage: Make sure all signs are clearly visible and well-maintained.
When Should You Test Your Equipment?
Timing is crucial. You don’t want to be scrambling to fix issues on your grand opening day. Here’s a timeline for testing:
During Installation
As your car wash equipment is being installed, conduct preliminary tests after each component is set up. This allows you to catch any immediate issues and rectify them before moving on. It also allows you to see if the installer followed the plans correctly and made all the necessary connections.
Pre-Commissioning Testing
Once installation is complete but before your “official” opening, perform thorough tests of the entire system. This includes water flow tests, chemical dispensing tests, and full wash cycle tests. We want to iron out all the issues at this phase.
Mock Run
Conduct several “mock runs” with staff members acting as customers. These simulations are incredibly valuable for identifying any issues that might not be apparent during isolated component tests. You can try different scenarios, such as a slow wash or a high-volume situation, to ensure your equipment performs consistently under various conditions.
Post-Opening Checkup
Even after your grand opening, implement a regular maintenance schedule that includes periodic equipment checks. This proactive approach is key to preventing long-term issues and ensuring the longevity of your car wash system. Daily, weekly, and monthly checks will keep your equipment in excellent working condition.
How to Conduct Effective Equipment Tests
Now, let’s delve into the practical “how” of testing your car wash equipment. Here’s a step-by-step guide:
Develop a Detailed Checklist
Don’t rely on memory. Create a detailed checklist for each piece of car wash equipment you need to inspect. This should include specific steps, metrics, and space for recording results. The checklists should be easy to use and understand. Consider creating a master checklist that can be used on each test, or you can create separate checklists for each type of equipment.
Gather Necessary Tools and Supplies
Ensure you have all the tools and supplies needed for testing, including pressure gauges, measuring cups, a multimeter, and basic hand tools. Having everything on hand will speed up your testing process. Make a list before you start and have a designated place where all the tools and equipment are stored.
Follow the Manufacturer’s Instructions
Always refer to the manufacturer’s manuals for the correct procedures for testing and maintenance of your car wash equipment. This will ensure that you are performing tests the correct way. Not following the instructions can cause damage to the equipment and void any warranty.
Start with the Basics
Begin with simple checks, like inspecting hoses for leaks and making sure the water pressure is adequate. Once you have made the simple checks then move to more complicated tests. Don’t forget to test the operation of each system independently before combining them for a full wash cycle test.
Conduct Full Wash Cycle Tests
After checking each component individually, run a complete wash cycle. Observe the entire process and look for any issues with water flow, chemical dispensing, drying, or any other areas. This is an opportunity to ensure all the systems are working together smoothly. Use your staff as mock customers. Have them drive through several times and give you feedback.
Record and Document Everything
Document all tests performed, results obtained, and any corrective actions taken. This detailed record-keeping will help you track patterns and make informed decisions. A detailed report will show you trends and allow you to catch issues before they become bigger problems. You can also use this information for regular maintenance schedules.
Address Any Issues Immediately
Don’t delay repairs or adjustments. Any problems identified during testing should be corrected immediately, and the equipment should be tested again before opening. Don’t open until all the issues are addressed and the equipment is working as expected.
Train Your Staff
Ensure your staff is properly trained on how to operate and maintain your car wash equipment. They should understand basic troubleshooting techniques and be able to address minor issues as they arise. Staff training should include how to conduct a daily walk-through and identify potential problems before they occur.
Develop a Maintenance Plan
Implement a regular maintenance schedule that includes periodic equipment checks. This proactive approach is critical for preventing long-term issues and ensuring the longevity of your car wash equipment.
Example Testing Scenario: Soap Dispenser
Let’s illustrate the testing process with a specific example: testing your soap dispenser:
- Check Connections: Make sure the soap delivery lines are securely connected and free of any visible damage or leaks.
- Verify Dilution Ratios: Use a measuring cup to collect soap dispensed over a timed interval. Check that the output matches the manufacturer’s recommended dilution ratio. If needed, make any necessary adjustments.
- Test Multiple Times: Repeat the test several times to ensure consistency.
- Record Results: Record the results in your checklist, including any observations or adjustments made.
- Troubleshoot: If any issues are found, such as inconsistent dispensing, identify the source of the problem (clogged lines, low soap level, faulty pump) and rectify it.
- Re-test: After troubleshooting, conduct a final test to ensure the problem is fixed and the soap dispenser is working properly.
Learn Business: Your Partner in Car Wash Success
Now, imagine having all the tools and templates you need to ace your pre-opening preparations. That’s where Learn Business comes in. Learn Business is designed to provide you with all the guidance you need to succeed.
Learn Business offers a variety of resources tailored to your business needs, including:
- Detailed Checklists: Ready-to-use checklists that you can use to ensure no detail is overlooked during your car wash testing process.
- Maintenance Schedules: Customizable templates for creating a comprehensive maintenance plan.
- Financial Templates: Tools to help you track your financials. These can help you manage your finances with ease and can provide valuable insights into your operations.
- Staff Training Documents: Documents that you can use to train your staff on equipment operations and maintenance procedures.
- Business Plans: Access to business plan templates that can help you create a well-structured plan for your car wash business.
- Marketing Materials: Templates to assist with your marketing strategies.
Learn Business is designed to support businesses like yours. We are your trusted partner to guide you through every step of the process.
Final Thoughts
Thoroughly testing your car wash equipment before opening is not just a good practice; it’s a necessity. It’s an investment in your business’s future, ensuring smooth operations, happy customers, and a healthy bottom line. By understanding the “why,” “what,” “when,” and “how” of equipment testing, you’ll be well-prepared to launch a successful and thriving car wash business. Don’t cut corners and take shortcuts, because your long-term success depends on it. And don’t forget, Learn Business is here to support you every step of the way! Now go make those cars sparkle!
Leave a Reply